Aluminum guitars have continued to be manufactured by various luthiers and companies over the years, and are often prized for their unique tonal characteristics, sustain, and striking aesthetic. While not as widely available as wooden guitars, they have carved a niche for themselves in the market for those looking for unconventional and innovative instrument designs.
Today, modern luthiers like David Giot continue to explore the possibilities of aluminum in guitar making, pushing the boundaries of design and sound in the process. Their commitment to craftsmanship and ability to incorporate aluminum into their instruments contribute to the ongoing history and development of aluminum guitars in the music industry.
From the bustling noise rock scene to the world of aluminum guitars, David Giot has had a remarkable journey as a luthier. With a background in Science and IT, David’s passion for music and instruments led him to explore the world of guitar making. His fascination with aluminum neck guitars eventually led him to develop his own prototypes and establish TTTides guitars. In this interview, David shares his experiences, challenges and unique approach to creating personalized instruments. Join us as we delve into the creative mind of David Giot and discover the artistry and innovation behind his aluminum axes.
Can you tell us something about yourself and your career as a guitar maker?
My name is David Giot and I am 44 years old. I grew up in Cherbourg, Normandy, France.
Almost all of my parents and friends worked in the submarine industry.
Passing on their knowledge about metals and alloys is still very helpful for my construction technology today. I studied technical drawing, mathematics and machine automation in Rennes (Brittany, France) and later worked for the Space Agency in Munich and on projects for the European Commission in Luxembourg.
When did you first develop an interest in music and instruments and what sparked your passion for building guitars?
The noise rock scene in Cherbourg and Rennes was huge and I had the chance to share the same passion with many people (Big up to Kfuel!, Studio Chaudelande).
I’ve played guitar in various noise rock bands and dreamed of one day owning an aluminum neck guitar. I ended up building my own aluminum neck guitar in my garage with the help of my dad and building more prototypes for my friends who played in loud rock bands. That was 18 years ago.
Also, until now and since 2004 I have had a small record label called Whosbrain Records; This was obviously a way to build a good relationship within the noise rock community.
Can you share with us your training and education journey in this field including any courses, workshops or training you have taken?
I learned how to use CNC automation machines at school, how to use 3D design software programs, but I also learned new techniques on my own, etc.
The internet is a wonderful way to learn something. I have done many things
Developed prototypes and practiced various techniques for 15 years before TTTides guitars were released. A lot of trial and error was done back then.
Can you walk us through your journey to becoming a professional luthier, including the challenges you faced and how you overcame them?
After a career in science and IT, I wanted to have more control over my life, so my girlfriend suggested I try what I’ve always wanted to do, which is to build neck instruments out of aluminum.
I also got support from Heiko from OKKOFX and Don Vito, who I occasionally have a beer with when they’re on tour (cheers, Heiko!).
He tried my first Model02 prototype, liked it, and then promoted the brand on a nice forum on Facebook called Aluminum Axts.
As for the challenges: To be honest, they initially consisted of creating a good working environment. Sometimes it is still difficult to organize the workshop well because I have never worked in such an environment as an apprentice. But I try to improve my cleaning and ordering every day.
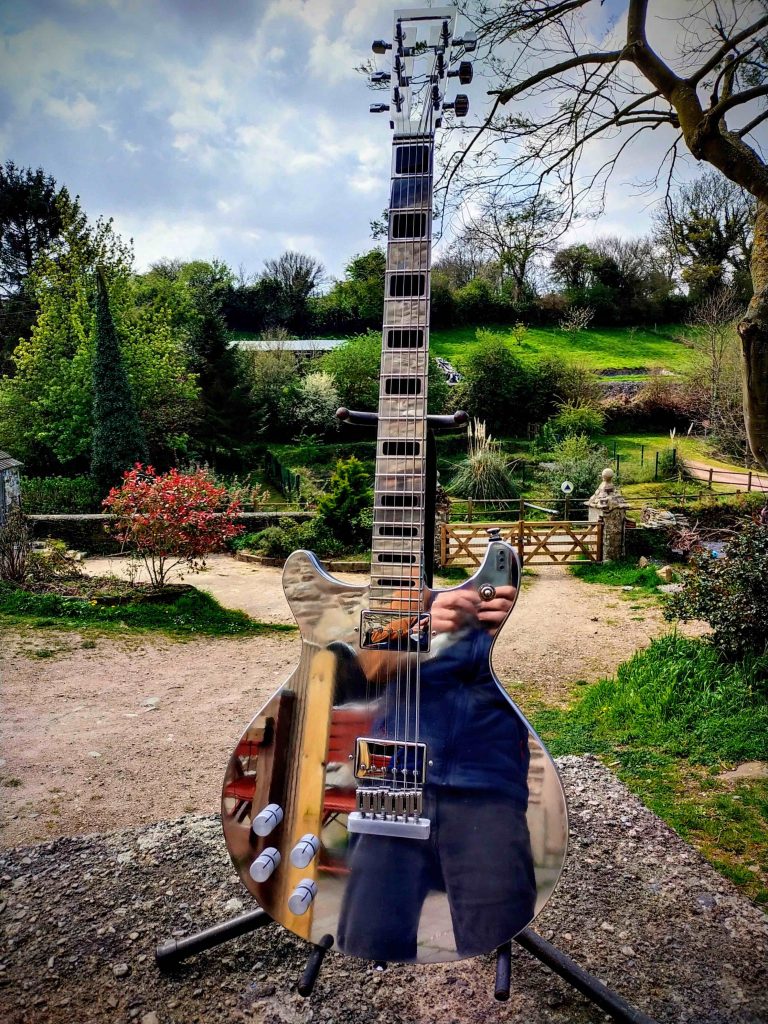
Can you describe your signature style and what makes your guitars different from others?
I mainly think aluminum guitars should have a thru-neck.
So 95% of my guitars have a neck-thru, and even a bit more because the aluminum goes from the headstock to the end of the body.
I also came up with the panfront aluminum design, a guitar where the neck and front of the body are machined from a large piece of aluminum. The headstock is also quite unique. And everything can be customized except for the spindle plate.
Can you share with us your experience with custom builds and your approach to working with customers to create a unique and personalized guitar?
I don’t follow a click-and-buy approach (although I may have to go that route soon). I prefer talking to the customer about their needs etc. So I like to refine the specs with people about their project (most of the time they know what they want anyway).
But with custom guitars, having to talk to the customer before they buy is a natural way to filter out compulsive buying. The waiting list also serves to ensure that customers want their custom guitars 100%.
I really don’t want to contribute to flooding the world with aluminum guitars (don’t get me wrong, they’re beautiful, but they have to remain unique in a way).
I also want to stay competitively priced, these guitars are quite expensive but I’m trying to make them “affordable”.
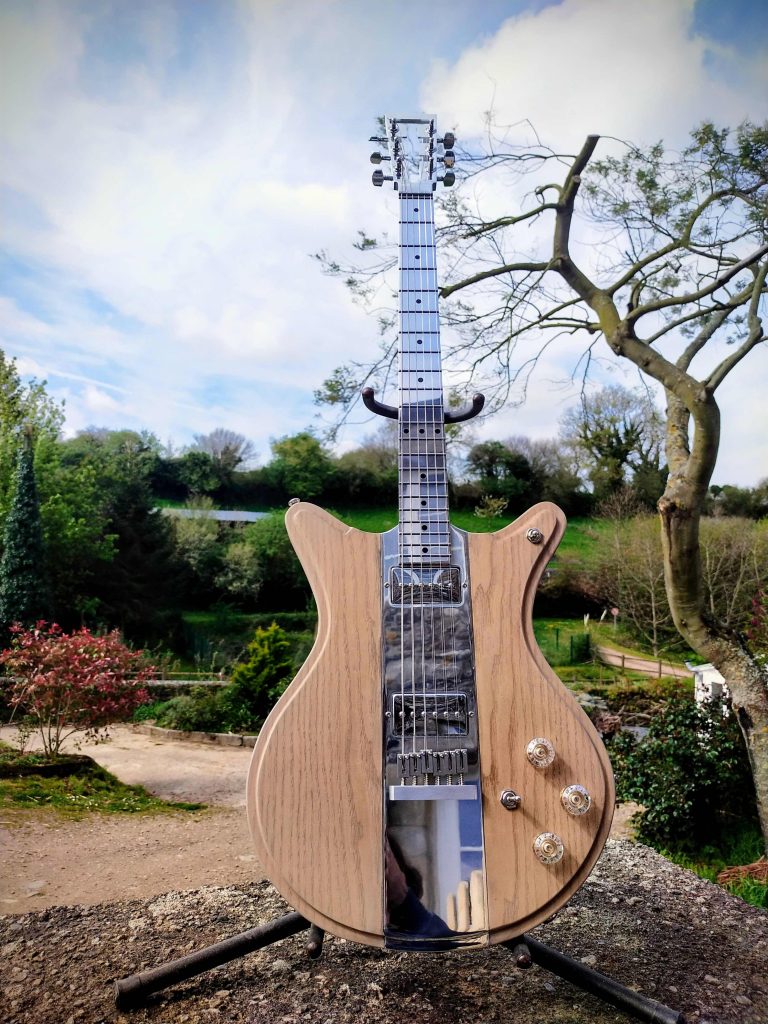
What are some of the greatest challenges and rewards of being a luthier, and how do you balance the creative and technical aspects of the craft?
The biggest challenge is paying attention to every detail. The processing of a guitar and the subsequent finishing by hand is also a risky business 🙂
But seeing my guitars played live by bands I listen to and admire is really rewarding. It’s also something special when customers order several guitars from me.
This is how you build a unique relationship.
Most of the creativity comes from the customer themselves; I don’t take note of these crazy ideas. I just try to implement them as best as possible.
What are your future goals for your company and do you have any new projects or cooperations planned?
My goal is simple: try to continue my path with no growth and no craziness. Of course I’m trying to improve my workshop and improve my workflow.
I’d like a little more time to try new things, like some aluminum semi-hollow guitars (cheers Laurie!).
The collaborations with bands continue and there will be more to come (although I’m a bit late with that…).
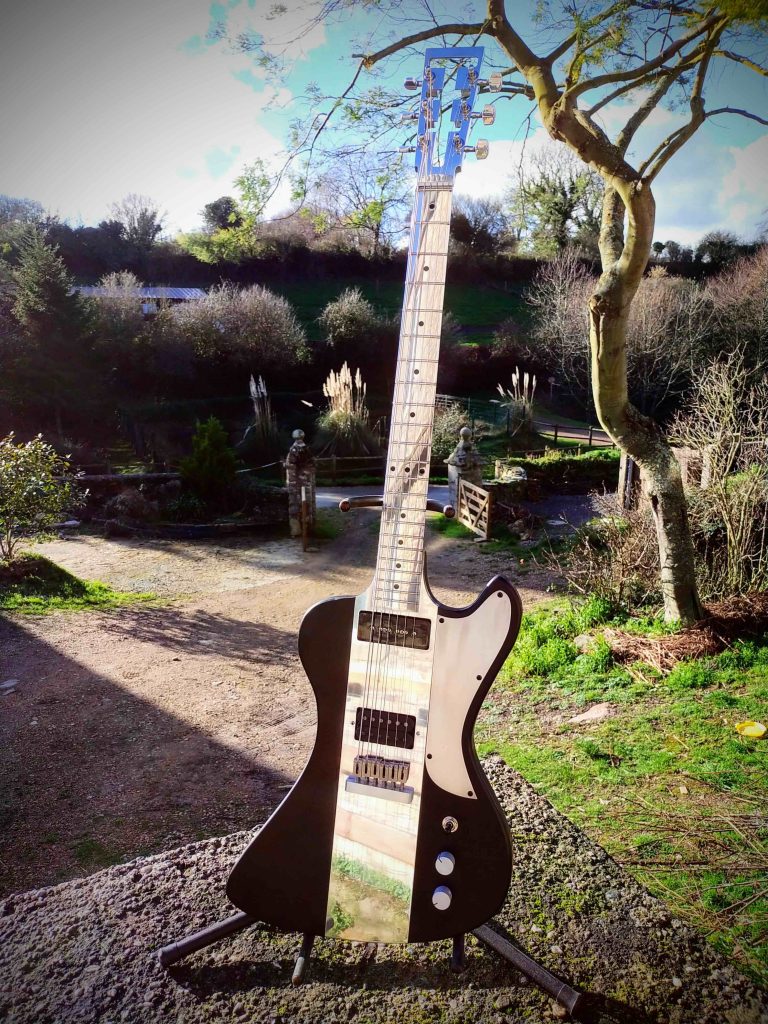
Finally, do you have any final thoughts or advice for aspiring luthiers, particularly those interested in incorporating aluminum into their work?
If you want to delve into building aluminum instruments, do so with good reason. Music and life around music should always be the main motivation for making instruments.
I don’t think there are any particular rules for going into this; It can be done with CNCs but also by hand, why not.
Applause !
Thank you for joining us on this insightful journey into the world of luthier David Giot and his remarkable aluminum guitars. We hope you have been inspired by his passion, dedication and innovative craftsmanship. From humble beginnings to becoming a renowned figure in the music industry, David’s story reminds us of the transformative power of following your dreams.
We sincerely thank you, our valued viewers, for taking the time to review this interview. Your support and engagement fuels our commitment to bringing you compelling stories and interviews. We invite you to continue exploring the rich spectrum of music, art and craftsmanship that resonates in the world of guitar making. Thank you for being part of our journey.